This you didn´t know about densifiers
The goal of all concrete densifiers
The goal of all concrete densifiers (Lithium, Sodium, Potassium, and Colloidal silica) is to deliver a reactive form of silica down into the microscopic pore system of the cement paste. All densifiers have the “same” chemistry varying only by the alkali used for solubility of the SiO2 (Silica). The differences are in the particle form and size of the silica and how the silica is made to stay in the liquid.
Densifiers are chemicals designed to react with free lime/calcium hydroxide (CH), resulting in a gel that consists of a calcium silicate hydrate. Free lime/Calcium hydroxide is a byproduct of the process of curing concrete. Hydrated lime can constitute up to 25 percent of hardened cement but adds no strength to the concrete. In all densifiers, the primary reaction happens between the free lime and the silica or silicates. The gel binds to the concrete and dries hard, making the concrete more durable and denser than it was before the application of the densifier.
Why Concria Nano Silica finishing aid is a much better option than sodium silicates?
Sodium and potassium densifiers are compounds of silicon and a high proportion of mineral salts. (Sodium silicate molecules, for example, are 38 percent sodium by weight and only 62 percent silica. When Sodium silicate densifiers release silica to form CSH, they leave behind the mineral salts. This is why sodium silicate and potassium silicate cannot be applied during the placement. Sodium silicates can be applied after 28d after casting and must be scrubbed off very well, to prevent the residual salts from forming hard, discoloring deposits.
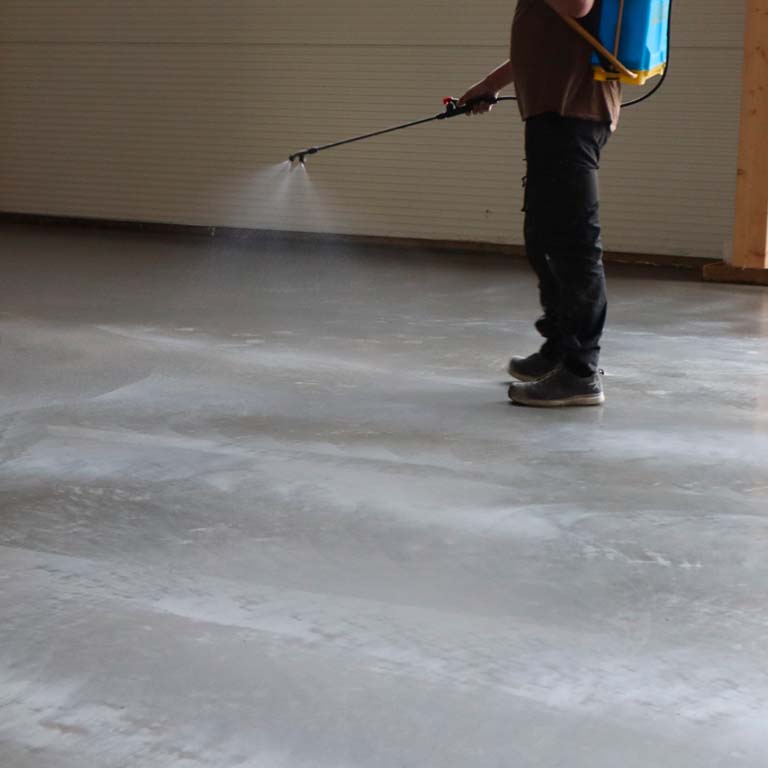
Concria Nano Finish is 99.5 percent pure silica and was developed to apply during the placement. This allows for easier, faster application and time savings. Concria Nano Silica finishing aid delivers virtually pure silica in nanoparticles small enough to penetrate the pore structure. The nano-sized silica particles have a lot higher proportion of reactive surface than silicates, so they react very rapidly and efficiently.
Nano Silica creates a new CSH that bonds to the existing CSH. Nano silica also bonds directly to all other silica, including itself. When applied to concrete, it reacts and then uses that bonded silica as a platform for additional bonding. Other Silicate densifiers do not do this.
The goal of all concrete densifiers
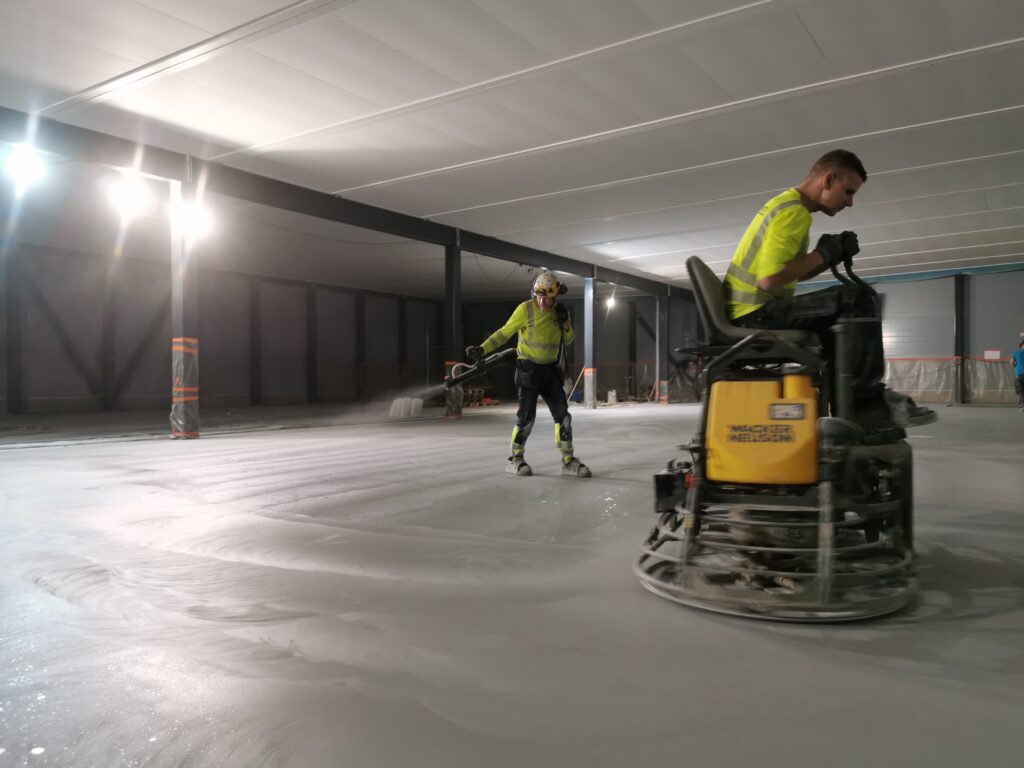
The goal of all concrete densifiers (Lithium, Sodium, Potassium, and Colloidal silica) is to deliver a reactive form of silica down into the microscopic pore system of the cement paste. All densifiers have the “same” chemistry varying only by the alkali used for solubility of the SiO2 (Silica). The differences are in the particle form and size of the silica and how the silica is made to stay in the liquid.
Densifiers are chemicals designed to react with free lime/calcium hydroxide (CH), resulting in a gel that consists of a calcium silicate hydrate. Free lime/Calcium hydroxide is a byproduct of the process of curing concrete. Hydrated lime can constitute up to 25 percent of hardened cement but adds no strength to the concrete. In all densifiers, the primary reaction happens between the free lime and the silica or silicates. The gel binds to the concrete and dries hard, making the concrete more durable and denser than it was before the application of the densifier.
Why Concria Nano Silica finishing aid is a much better option than sodium silica?
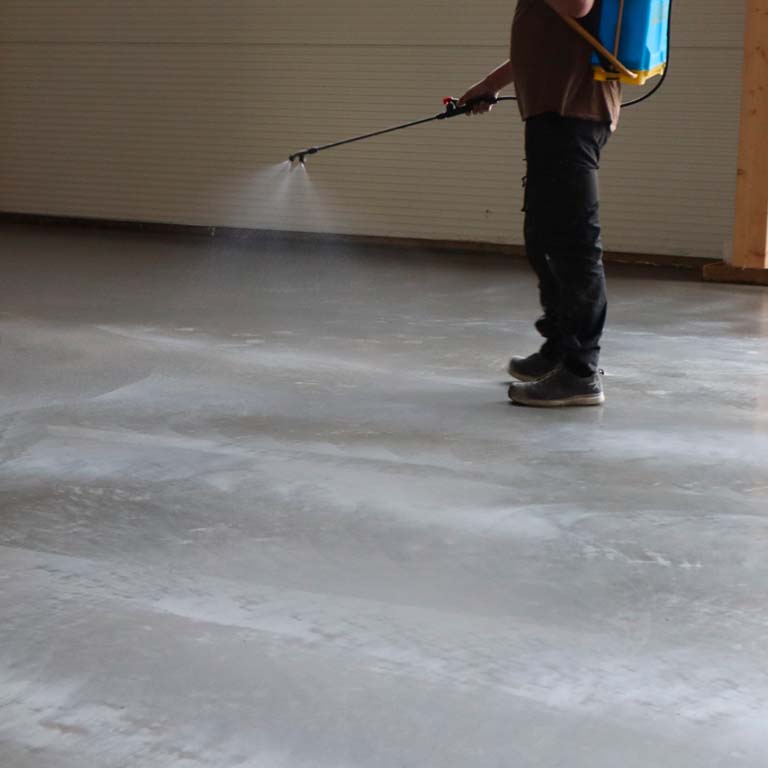
Sodium and potassium densifiers are compounds of silicon and a high proportion of mineral salts. (Sodium silicate molecules, for example, are 38 percent sodium by weight and only 62 percent silica. When Sodium silicate densifiers release silica to form CSH, they leave behind the mineral salts. This is why sodium silicate and potassium silicate cannot be applied during the placement. Sodium silicates can be applied after 28d after casting and must be scrubbed off very well, to prevent the residual salts from forming hard, discoloring deposits.
Concria Nano Finish is 99.5 percent pure silica and was developed to apply during the placement. This allows for easier, faster application and time savings. Concria Nano Silica finishing aids delivers virtually pure silica in nanoparticles small enough to penetrate the pore structure. The nano-sized silica particles have a lot higher proportion of reactive surface than silicates, so they react very rapidly and efficiently.
Nano Silica creates a new CSH that bonds to the existing CSH. Nano silica also bonds directly to all other silica, including itself. When applied to concrete, it reacts and then uses that bonded silica as a platform for additional bonding. Other Silicate densifiers do not do this. Reactive Concria Nano Finishing aid even bonds to and hardens decorative cementitious overlays that are low-lime, traditional silicate densifiers will not do this.
Concrete or dry shake hardeners cannot be densified during the casting?
You may have heard many times that concrete floors cannot be densified during casting because there is not enough calcium hydroxide available. This is incorrect, because Differential thermal analyses of hardening cement paste, show that crystalline calcium hydroxide (CH) begins to form after 4 hours’ reaction (water mixed with cement). Thereafter, the crystallization proceeds rather rapidly. Concria finishing aid is a nano-silica liquid that is sprayed during the floating and finishing with blades, so there is a lot of CH available for reaction.
Nano Silica reacts with free lime/CH and increases final cement hydration rate alot. Typically the maximum hydration rate of cement is 75%, whereas with Nano silica we can reach almost 90% and that’s the key reason why with Concria Nano Silica we get harder and denser concrete surfaces. There is no need for any other densifier later, like the Sodium or lithium densifiers. Using Concria Nano Silica is also less expensive than applying densifiers 28d after casting.
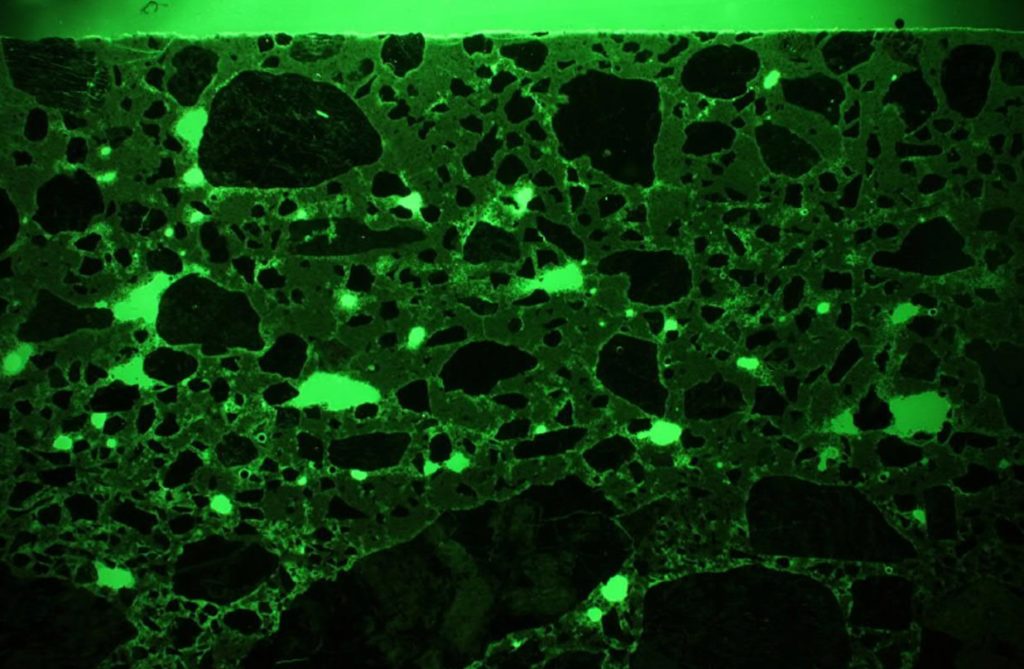
Concrete or dry shake hardeners cannot be densified during the casting?
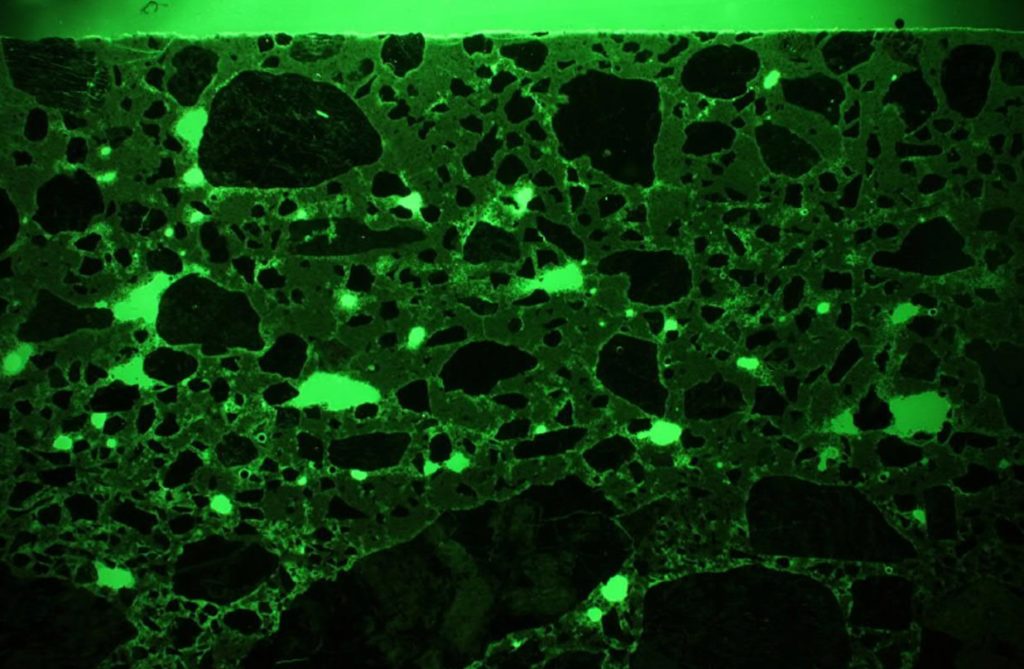
You may have heard many times that concrete floors cannot be densified during casting because there is not enough calcium hydroxide available. This is incorrect, because Differential thermal analyses of hardening cement paste, show that crystalline calcium hydroxide (CH) begins to form after 4 hours’ reaction (water mixed with cement). Thereafter, the crystallization proceeds rather rapidly. Concria finishing aid is a nano-silica liquid that is sprayed during the floating and finishing with blades, so there is a lot of CH available for reaction.
Nano Silica reacts with free lime/CH and increases cement hydration rate a lot. Typically the maximum hydration rate of cement is 75%, whereas with Nano silica we can reach almost 90% and that’s the key reason why with Concria Nano Silica we get harder and denser concrete surfaces. There is no need for any other densifier later, like the Sodium or lithium densifiers. Using Concria Nano Silica is also less expensive than applying densifiers 28d after casting.
Contractors should stop using water during the placement
Spraying water during the finishing can be detrimental to concrete performance.
”Blessing” the concrete with water weakens the surface and the added water gets encapsulated in microscopic pores in the hardening surface, later evaporating to leave behind voids that make the concrete surface less dense and strong. Sprayed water will increase the W/C ratio on top of the surface and will affect the durability and abrasion resistance. Concria advanced Nano Finish can be sprayed during the casting, and it will increase cream, making for easier, better finishing and extended workable time under adverse conditions and making the surface much more durable than finishing with water.
Works as a evaporate retarder
According to a water retention efficiency test, Concria Nano Silicas slows evaporation by nearly 20% and protects the concrete and dry shake hardeners from a range of moisture loss-related defects like delamination, plastic shrinkage, map-cracking, and other surface defects.
Contractors should stop using water during the placement
Spraying water during the finishing can be detrimental to concrete performance.
”Blessing” the concrete with water weakens the surface and the added water gets encapsulated in microscopic pores in the hardening surface, later evaporating to leave behind voids that make the concrete surface less dense and strong. Sprayed water will increase the W/C ratio on top of the surface and will affect the durability and abrasion resistance. Concria advanced Nano Finish can be sprayed during the casting, and it will increase cream, making for easier, better finishing and extended workable time under adverse conditions and making the surface much more durable than finishing with water.
Works as a evaporate retarder
According to a water retention efficiency test, Concria Nano Silicas slows evaporation by nearly 20% and protects the concrete and dry shake hardeners from a range of moisture loss-related defects like delamination, plastic shrinkage, map-cracking, and other surface defects.
WHY USE CONCRIA NANO-SILICA:
- To increase cream for a better, easier and faster finish
- To Minimize the risk of plastic shrinkage, map-cracking and other surface defects
- To densify concrete surface during the casting.
- Speed up the construction schedule
- To get the dustproof surface during the placement
- If you mechanically grind/polish the floor you don’t need to apply densifiers during the polishing process
- To extend the workability of the slab surface
- To achieve the best possible finish
- To eliminate the need for additional water
- To receive lower RA and higher DOI numbers
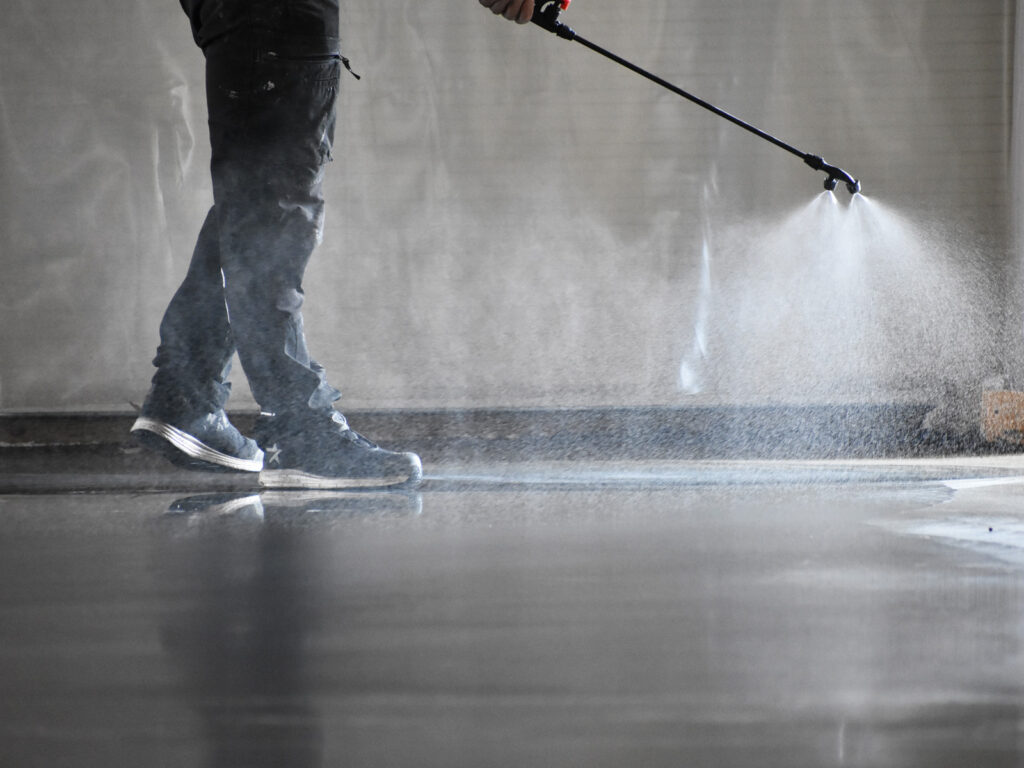
Also using a Nano silica finishing aid during the finishing multiple times it will contribute a greater amount of cement particle-to-particle packing that then contributes to an increase in gloss, smoothness, hardness, and abrasion resistance. Burn finished concrete/dry shake surface with Concria Nano Finishing aid can be as smooth as polished concrete with 3000# diamond, under 20μin in Ra meter (scientific roughness measurement)
WHY USE CONCRIA NANO-SILICA:
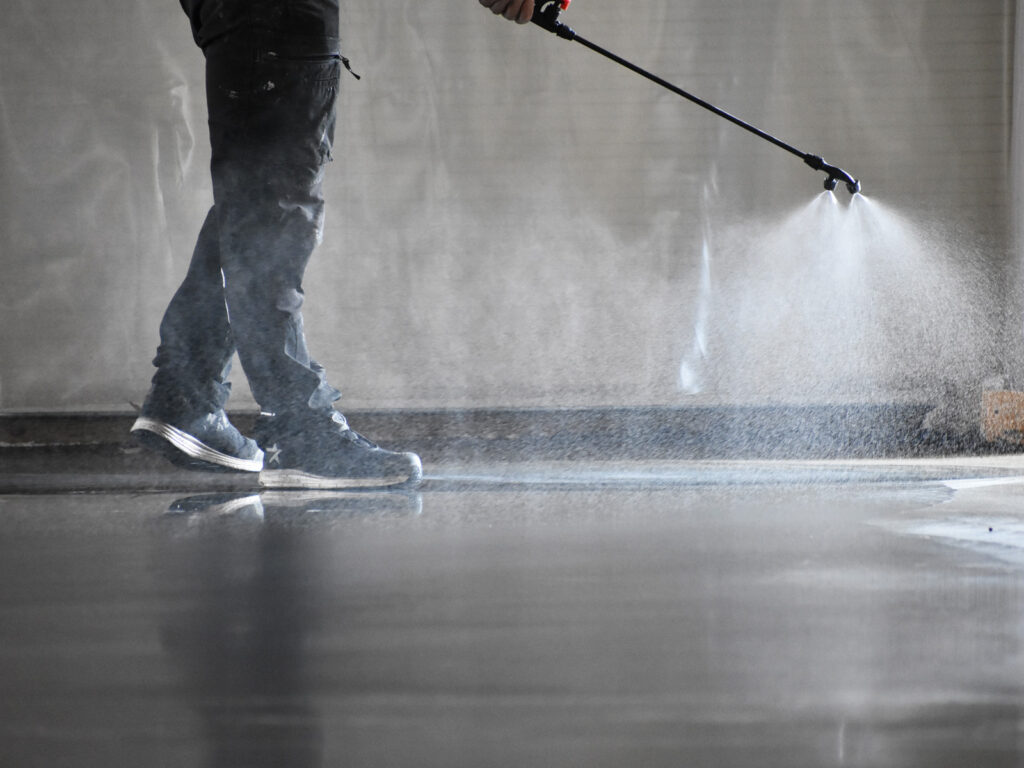
- To increase cream for a better, easier and faster finish
- To Minimize the risk of plastic shrinkage, map-cracking and other surface defects
- To densify concrete surface during the casting.
- Speed up the construction schedule
- To get the dustproof surface during the placement
- If you mechanically grind/polish the floor you don’t need to apply densifiers during the polishing process
- To extend the workability of the slab surface
- To achieve the best possible finish
- To eliminate the need for additional water
- To receive lower RA and higher DOI numbers
Glossier Finish
Also using a Nano silica finishing aid during the finishing multiple times it will contribute a greater amount of cement particle-to-particle packing that then contributes to an increase in gloss, smoothness, hardness, and abrasion resistance. Burn finished concrete/dry shake surface with Concria Nano Finishing aid can be as smooth as polished concrete with 3000# diamond, under 20μin in Ra meter (scientific roughness measurement)
If you would like more information, please get in touch with our sales team at: [email protected]
Mika Ahonen
CTO and Founder of Concria
READ MORE ABOUT OUR SOLUTIONS & DENSIFIERS
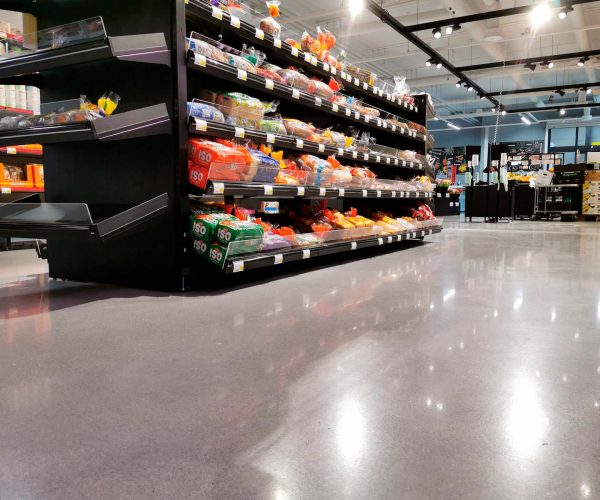
Concria OPTIMAL SLAB™ Deco Decorative polished concrete topping
For extremely tight timeframes and budgets
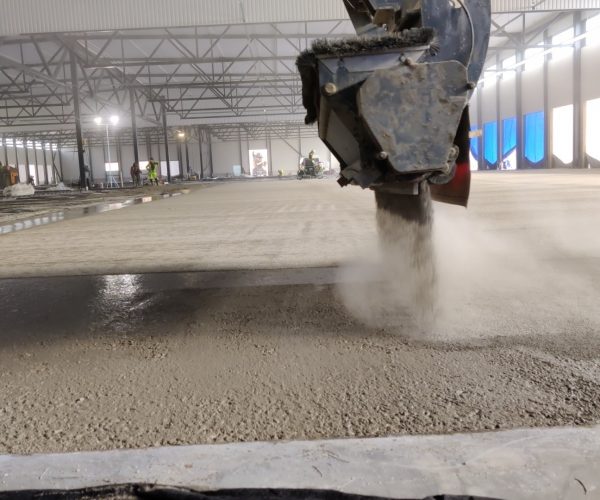
Concria OPTIMAL SLAB™ Industrial New generation dry-shake hardener floor
Better bonding. More uniform color. Minimized shrinkage. No Delamination.
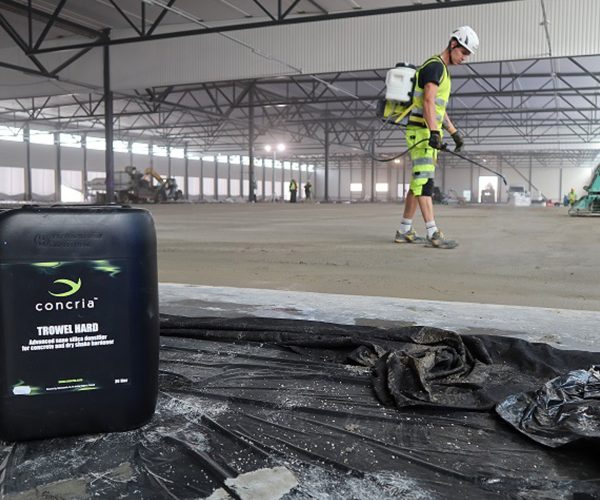
Concria™ Trowel Hard densifier for dry shake floors
Densify dry shake floor during the casting